Trending: Here are some Business Statistics and Trends to know
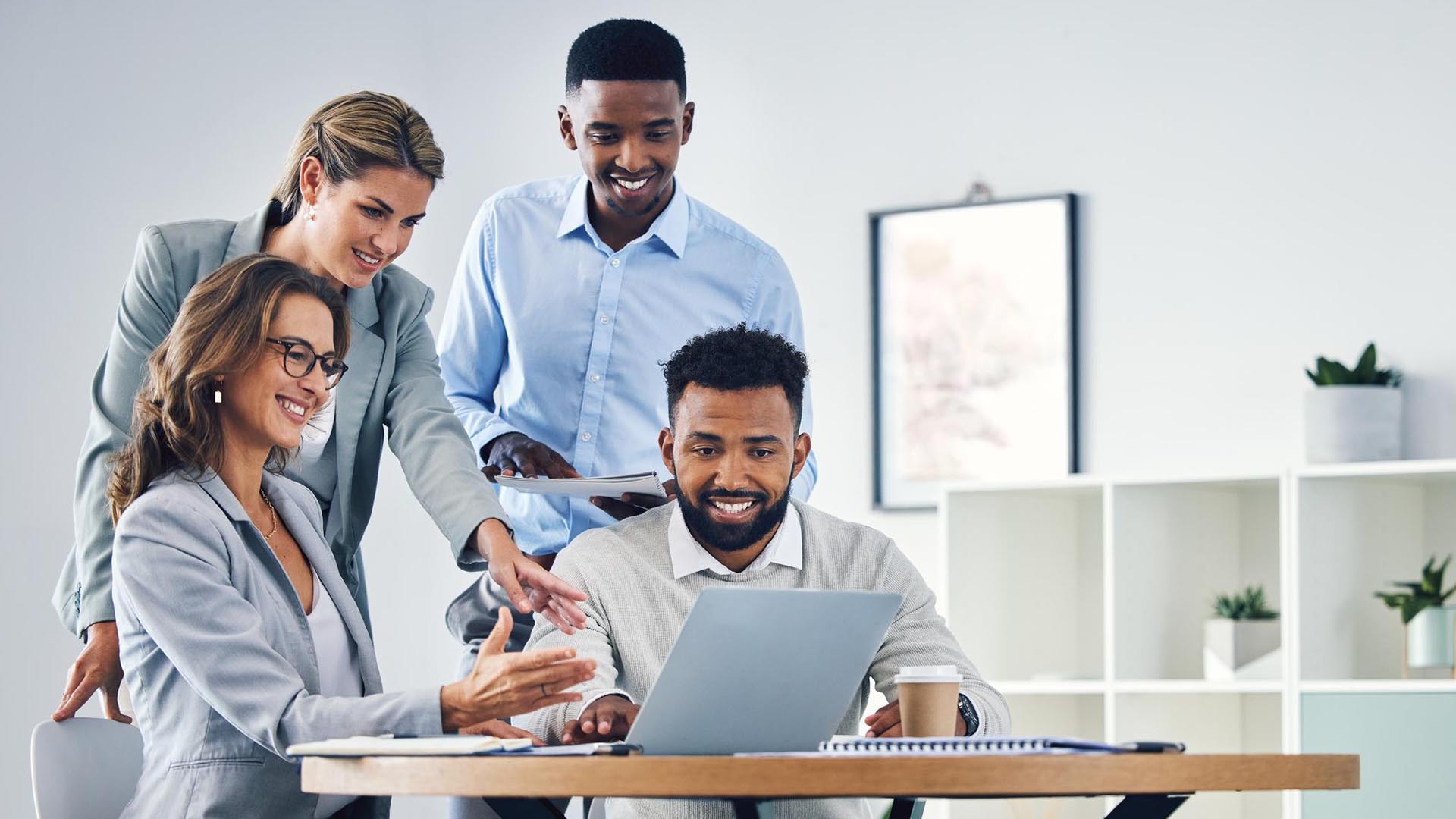
Getting your Trinity Audio player ready...
|
Have you ever wondered how businesses efficiently produce and deliver goods and services? The answer lies in effective operations management processes.
From manufacturing to service industries, operations management is vital in the operation manager of a production facility optimizing processes and achieving organizational goals.
Operations management is a field that focuses on the design, planning production management, and control of business operations. It oversees resources, processes, and systems to ensure maximum efficiency and productivity. While often overlooked, operations management is the backbone of any successful business.
In today’s competitive business landscape, organizations that prioritize operations management gain a significant edge over their competitors. From cost reduction to improved customer satisfaction, the benefits of proper operations management are numerous and far-reaching.
In this article, we will explore the various advantages businesses can enjoy by effectively implementing operations management principles.
Operations Management
Operations management (OM) is the administration of operational management of business practices to create the highest level of efficiency possible within an organization.
What is Operations Management?
Operations management is the systematic design of project management, control, and improvement of an organization’s processes and activities to achieve desired outcomes efficiently and effectively. It encompasses a top operation manager’s wide range of responsibilities, from overseeing the production of goods and delivery of services to managing the supply chain, resources, and workforce.
At its core, operations management is about optimizing the processes and systems that transform inputs (such as raw materials, information, and labor) into outputs (products or services) while minimizing waste and maximizing value. It is a multifaceted discipline that requires a holistic view of an organization’s internal and external factors in operations.
Key components of operations management include:
- Process Design and Improvement: Operations managers analyze existing processes, identify bottlenecks, and design efficient workflows. Continuous improvement methodologies like Lean and Six Sigma are often employed to streamline operations and reduce waste.
- Quality Control: Ensuring consistent quality in products or services is paramount. Operations management involves setting quality standards, implementing quality control measures, and addressing deviations from these standards.
- Resource Allocation: Efficient allocation of resources, including human resources, machinery, and materials, is a critical aspect. Operations managers must balance resource availability with demand to optimize efficiency.
- Supply Chain Management: Managing the end-to-end supply chain, from sourcing raw materials to delivering final products to customers, is a key function. This includes supplier relationships, inventory management, and logistics.
- Inventory Management: Controlling and optimizing inventory levels to meet demand while minimizing holding costs is essential. Operations managers use various techniques to strike this balance.
- Capacity Planning: Determining the capacity needed to meet demand is a strategic aspect of operations management. It involves analyzing demand forecasts and adjusting production or service capacity accordingly.
- Risk Management: Identifying and mitigating operational risks, such as supply chain disruptions or process failures, is vital. Contingency plans and risk assessment are standard tools in this regard.
- Strategic Decision-Making: Operations managers provide data-driven insights to support strategic decisions. They align operations with overall business objectives and contribute to long-term planning.
- Customer Focus: Customer satisfaction is a core goal. Operations management ensures that products or services meet or exceed customer expectations through consistent quality, timely delivery, and responsiveness.
- Efficiency Metrics: Key performance indicators (KPIs) and metrics are used to measure and track the performance of operations. These metrics provide insights for continuous improvement.
Operations management is not limited to manufacturing; it applies to all industries, including service-oriented businesses. Its principles are adaptable and scalable, making it a fundamental discipline for organizations of all sizes.
In today’s fast-paced and competitive business environment, effective operations management is a cornerstone of success, allowing businesses to meet customer demands, reduce costs, and stay agile in a dynamic market.
Why is Operations Management the Core of Every Business?
Operations management has evolved into the nucleus of nearly every organization. Within a company, numerous fundamental business functions come into play. These encompass crucial aspects such as manufacturing, distribution, and the delivery of goods and services.
Operations management serves as the linchpin that the operations manager ensures these functions run with maximum efficiency, enabling the fulfillment of customer needs. This intricate interplay of operations not only ties an organization to its customers but also forms the connective tissue binding together its clients, suppliers, and employees.
Efficiently managing operations is pivotal, as any shortcomings in this area can give rise to a multitude of challenges for businesses. Ineffectively managed operations can hinder employees from performing their duties or meeting customer requirements effectively, ultimately impacting the overall business success of the organization.
Benefits of Operations Management
Operations management serves as the linchpin of a production system that holds an organization together, ensuring that its various components work harmoniously to achieve strategic goals.
In this section, we explore the tangible benefits that businesses and professionals like you can reap from effective operations management.
1. Improved Efficiency
Efficiency is the lifeblood of any successful business and operation management is. As a seasoned professional and operations manager, you understand that wasted time and resources can erode profits and hinder progress. Operations management, when implemented effectively, is a beacon of efficiency.
By streamlining processes and workflows, operations management ensures that every task is performed with maximum efficiency. Redundancies are eliminated through waste reduction, and the focus shifts toward achieving more with fewer resources. This, in turn, results in cost savings, increased revenue, and improved productivity.
Imagine a manufacturing process where every step of the production process is optimized, and unnecessary delays are eradicated. The result? Products are produced faster, costs are reduced, and customer orders are fulfilled promptly. Such efficiency not only saves time and money but also enhances your organization’s reputation for reliability and professionalism.
2. Cost Reduction
In the world of business, cost reduction is a perpetual goal. Operations management plays a pivotal role in achieving this goal. Through meticulous analysis and strategic decision-making, you can identify cost-saving opportunities that might have otherwise gone unnoticed.
Costs can be managed effectively by supervising operations more closely using production schedules, monitoring expenses, renegotiating supplier contracts, or even reconfiguring your supply chain. With operations management, you’re equipped to identify inefficiencies and implement changes that have a direct impact on your bottom line.
Real-world examples abound: companies that have successfully trimmed their operating costs through operations management have experienced substantial financial gains. These savings can then be reinvested in growth initiatives, research and development, or improving overall product quality elsewhere.
3. Quality Control
Quality control is not a mere checkbox; it’s a reflection of your commitment to excellence. Operations management provides the tools and methodologies necessary to ensure consistent quality in your products or services.
By establishing stringent quality assurance measures for production software, you can catch and rectify issues early in the production or service delivery process. This prevents defects, reduces rework, and ultimately results in higher customer satisfaction.
Consider this: a restaurant that meticulously monitors the quality of ingredients and cooking processes not only avoids costly errors but also builds a loyal customer base. People return because they know they can trust the consistent quality of the food and service.
In the competitive business landscape, a reputation for quality is invaluable. Operations management equips you to uphold that reputation and, in doing so, secure customer trust and loyalty.
4. Enhanced Productivity
Productivity is not just about doing more; it’s about doing more with the same or fewer resources. Operations management focuses on maximizing employee productivity and resource allocation.
As a business professional, you understand that your human capital is among your most valuable assets. Operations management provides tools and strategies to optimize the workforce.
This includes training, skill development, and efficient task allocation, all of the external factors that contribute to higher productivity levels.
Effective resource allocation, another cornerstone of operations management, ensures that your resources are used efficiently. Whether it’s machinery, raw materials, or technology, the goal is to minimize waste and maximize output.
Imagine a scenario where your employees are equipped with the skills, training programs, and tools they need to excel and your resources are used judiciously. The result is a workforce that performs at its peak, consistently delivering outstanding results for your business.
5. Supply Chain Optimization
For a business professional like yourself, the supply chain is a critical component of an operations management professional itself. Operations management takes the helm in optimizing this intricate network of suppliers, manufacturers, distributors, and retailers.
Effective supply chain management reduces lead times, minimizes inventory costs, and ensures the timely delivery of products or services to your customers. This supply chain process, in turn, enhances your ability to meet customer demand well, adapt to market fluctuations, and stay competitive.
Consider a retail company that manages its supply chain with precision. By using efficient, production processes, minimizing excess inventory, and ensuring just-in-time deliveries, they avoid unnecessary holding costs while always having products available for customers. This strategic approach to supply chain management not only lowers costs but also enhances customer satisfaction.
Operations management empowers you to fine-tune your supply chain, making it more agile and responsive to market changes. It’s a strategic advantage that ensures you can meet customer demands while maintaining a competitive edge.
7. Strategic Decision Making
Informed decision-making is the cornerstone of successful businesses. Operations management provides you with data-driven insights that guide your strategic choices.
By collecting and analyzing data on operations, you gain a deep understanding of your business’s strengths and weaknesses. This knowledge empowers you to align your operations with overarching business goals, making every decision a step towards growth and sustainability.
Imagine a tech company that regularly analyzes customer feedback, production metrics, and market trends. Armed with this data, they make informed decisions about product development, marketing strategies, and resource allocation. This strategic approach ensures they stay ahead of the competition and maintain profitability.
Operations management isn’t just about day-to-day operations; it’s about shaping your business’s future through informed and strategic decision-making.
8. Improves Customer Satisfaction
For a business to succeed, customer satisfaction is paramount. The operations management team plays a pivotal role in meeting and exceeding customer expectations.
By ensuring timely deliveries, consistent product or service quality, and responsive customer service, operations management helps build a loyal customer base. Satisfied customers not only return but also become advocates for your brand, driving growth through referrals and positive reviews.
Think of a software company that not only delivers reliable products but also provides excellent post-purchase support. This commitment to customer satisfaction not only retains existing customers but also attracts new ones through word-of-mouth recommendations.
Operations management is your tool for delivering on promises and creating lasting relationships with your customers. It’s a path to building a strong reputation and a loyal customer base.
9. Competitive Advantage
In the fiercely competitive business landscape, finding a competitive edge is a constant pursuit. Operations management offers you a significant advantage.
When you implement operations management strategies effectively, you not only reduce costs but also improve quality, productivity production efficiency, and customer satisfaction. This multifaceted approach positions your business as a leader in your industry.
Consider successful companies that attribute their dominance to operations management. They can offer competitive prices, high-quality products or services, and superior customer experiences. This trifecta of advantages creates a stronghold in the market.
As a business professional, you understand the value and importance of operations management in staying ahead of competitors. Operations management provides the tools to not only keep pace but also lead the pack in your industry.
Conclusion
In your journey as a business professional, operations management emerges as a critical asset, offering many tangible benefits. The efficiency it brings, the costs it reduces, the quality it ensures, and the productivity it enhances all contribute to your business’s success.
Supply chain optimization and risk management safeguard your operations against disruptions, while data-driven insights empower strategic decision-making. The ultimate goal is customer satisfaction, which, in turn, leads to a competitive advantage that sets you apart in your industry.
As you navigate the complex landscape of modern business, consider operations management not as an option but as a strategic imperative. Embrace its principles, harness its power, and watch as your business flourishes in the ever-evolving market. The benefits are not just theoretical; they are yours to realize through careful implementation and unwavering commitment to operational excellence.
Frequently Asked Questions (FAQs) about Operations Management
What are the Types of Operations Management (OM)?
- Operations Management (OM) encompasses various roles that play critical functions within an organization. The specific types of OM roles can vary significantly depending on the size and nature of the company. In some cases, operational managers may have diverse responsibilities, while in others, they might specialize in particular areas of expertise.
What are some Systems of Operations Management?
- Modern operations management is built upon several foundational theories and systems. While there are numerous theories, one of the commonly recognized frameworks for operations management includes four key theories. These theories provide the framework for understanding and improving operations:
- a. Total Quality Management (TQM): Focuses on continuous quality improvement and customer satisfaction.
- b. Lean Management: Aims to eliminate waste and increase efficiency in processes.
- c. Six Sigma: Concentrates on reducing defects and improving process consistency.
- d. Theory of Constraints (TOC): Identifies and mitigates constraints that limit an organization’s ability to achieve its goals.
These systems and theories serve as valuable tools for enhancing operational efficiency and effectiveness in various industries and settings.
What are the qualities of a good Operations Manager?
- Answer: Effective operations managers possess a combination of skills and qualities, including:
- a. Leadership Skills: They should be able to inspire and guide their teams, fostering a culture of collaboration and continuous improvement.
- b. Analytical Thinking: A good operations manager can analyze complex situations, make data-driven decisions, and identify areas for improvement.
- c. Communication Skills: Clear communication is crucial for coordinating various aspects of operations and ensuring everyone is on the same page.
- d. Problem-Solving Abilities: Operations managers must be adept at identifying and resolving challenges efficiently.
- e. Adaptability: They should be able to adjust strategies and tactics to meet changing business needs and market conditions.
- f. Attention to Detail: Precision is essential to ensure that operations run smoothly and efficiently.
What is the main purpose of operations management and why?
- Answer: The primary purpose of operations management is to ensure that an organization’s processes and activities are carried out efficiently and effectively to achieve its strategic goals. Operations management serves as the backbone of a business, facilitating the production of goods or delivery of services, managing resources, and optimizing processes. Its significance lies in:
- a. Efficiency: Operations management strives to minimize waste, reduce costs, and maximize productivity, which are essential for profitability.
- b. Quality: It ensures that products or services consistently meet or exceed customer expectations, enhancing customer satisfaction and loyalty.
- c. Competitiveness: Operations management gives businesses a competitive edge by enabling them to respond quickly to market changes and customer demands.
- d. Risk Mitigation: Identifying and addressing operational risks, helps organizations prepare for unforeseen challenges and maintain business continuity.
- e. Strategic Alignment: Operations management aligns day-to-day activities with the organization’s long-term strategic goals, contributing to its growth and sustainability.